INTRODUCCIÓN
El vertido no controlado de residuos y excedentes generados de las cosechas en el entorno rural constituyen un elemento de infección para los cultivos, así como contaminación mediante la quema1. Los materiales lignocelulósicos son elementos biodegradables importantes para la fabricación sustentable de biocombustible2. Éstos pueden procesarse según el concepto de biorrefinería, que involucra el tratamiento consecutivo y organizado para lograr un beneficio integral de los residuos. De esta forma, se logra reducirlos a una mínima o ninguna fracción de descarte con el consecuente respeto al medio ambiente3. El uso de material lignocelulósico de descarte constituye un recurso abundante y de reducido coste, que podría dar solución a los inconvenientes de su disposición final. Estos materiales están compuestos mayoritariamente por celulosa, hemicelulosa y lignina, los cuales, se disponen estructuralmente de manera entrelazada por uniones de tipo no covalente y covalente4.
Un azúcar reductor (dadores de electrones), se caracteriza por presentar un grupo carbonilo intacto, presentando funciones aldehído o cetona en forma libre, susceptible de ser oxidadas5. Dentro del grupo de azúcares reductores se cuenta con la glucosa, fructuosa, galactosa, manosa y maltosa6.
En este sentido la presente revisión no solo ofrece un compendio de técnicas y avances en la obtención y purificación de azúcares reductores, sino que también resalta su potencial para generar productos de alto valor añadido de manera sostenible. Con ello se promueve el desarrollo de tecnologías más verdes y la transición hacia una bioeconomía, contribuyendo a la valorización de residuos, minimizando el impacto ambiental y promoviendo la economía circular.
Materias primas y composición
La biomasa lignocelulósica es una matriz compleja compuesta de tres macromoléculas, como ser la celulosa, hemicelulosa, y lignina. La celulosa (C6H10O5)n es uno de los polímeros estructurales de la pared celular del reino vegetal, constituido de glucosas de 5000 a 15000 unidades7 entrelazadas por uniones β-(1-4) (8 siendo su cristalinidad una limitante en su hidrólisis9.
La hemicelulosa (C5H8O4)m son polisacáridos ramificados y heterogéneos que representan del 20-35% del peso de la biomasa vegetal10. Está constituida por unidades de cinco carbonos (xilosa, ramnosa y arabinosa), seis carbonos (glucosa, manosa y galactosa), y ácidos urónicos unidos por enlaces β-(1-4), y en menor medida por enlaces β-(1-3) glucosídicos11. Dependiendo de la fuente de donde provienen, la hemicelulosa presenta un intervalo de polimerización de 100 a 200 unidades. Presenta una cadena lineal de xilano con ramificaciones de ácido glucurónico, manano, galactomanano, glucomanano, entre otros12.
La lignina [C9H10O3(OCH3)0.9-1.7]x, es una estructura hidrofóbica, constituida de unidades fenilpropanoide (cumaril, guaiacil y siringil) y que representa del 15-40% de la biomasa vegetal. Se diferencian en la sustitución con el grupo metoxilo (-OMe) en las posiciones 3 y 5 de la unidad aromática. Esta sustitución otorga una configuración amorfa con alta heterogeneidad. La lignina se constituye en barreras protectoras de la biomasa contra la acción de microorganismos o degradación por agentes químicos13. La lignina se entrecruza con la hemicelulosa por varios enlaces químicos. Éstas encapsulan fuertemente la celulosa, formando una densa estructura matricial tridimensional14, y generando dificultades en la conversión del biopolímero sacarificado a etanol15. La disposición estructural de la celulosa, hemicelulosa y lignina en un material lignocelulósico se muestra en la Figura 1.
La representación porcentual de hemicelulosa, lignina y celulosa varían de acuerdo con la edad y tipo de planta17. Materias primas como la caña de azúcar, la cáscara de cereales, desechos forestales, residuos del café y de la elaboración de cerveza, constituyen un potencial para la generación de azúcares reductores18. En la Tabla 1 se muestra la representación porcentual de los constituyentes más representativos de fuentes vegetales.
Tabla 1 Representación porcentual de los constituyentes fisicoquímicos más representativos de fuentes vegetales
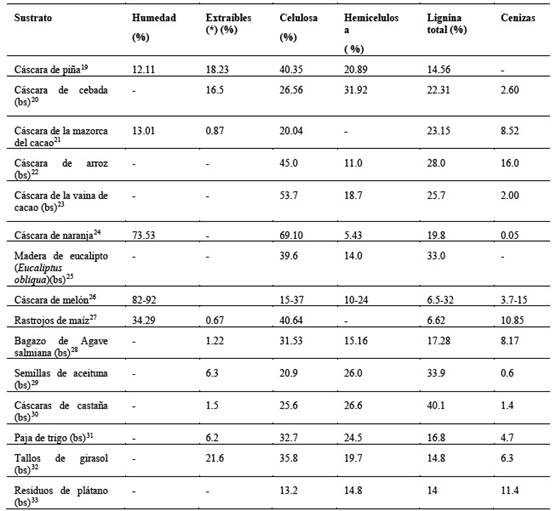
(*) Corresponden a proteínas, vitaminas, lípidos, minerales, clorofila, terpenos, resinas y fenoles.bs: base seca
A nivel polimérico los materiales lignocelulósicos se pueden disgregar en glucano, xilano, arabano y lignina; así como sus principales sustituyentes como los grupos acetilos y ácidos urónicos. Todos ellos se detallan en la Tabla 2.
Métodos de producción de azúcares reductores
El éxito de la biorrefinería para obtener azúcares reductores depende de la aplicación correcta de las metodologías tecnológicas a aplicar34. La contribución de biorrefinerías a la bio-economía futura inspira oportunidades comerciales basadas en la diversificación del producto mejorando su impacto medioambiental35. Entre las diversas formas de despolimerizar (ruptura de macromoléculas en unidades monoméricas o oligoméricas más pequeñas) la biomasa vegetal se encuentra la autohidrólisis, hidrólisis ácida, alcalina, enzimática y una combinación de las anteriores. En los procesos de hidrólisis se produce una reacción específica que implica la ruptura de enlaces químicos por la adición de agua36.
Autohidrólisis
También llamada “tratamiento con agua caliente comprimida”, es un proceso medioambientalmente amistoso y económico donde se emplea agua como único reactivo. Puede llevarse a cabo en intervalos de temperaturas de 190 a 225 ºC, y tiempos diversos, permitiendo principalmente la solubilización de hemicelulosas. Esto genera un incremento de la superficie de la biomasa y disminuye la cristalinidad de la fracción celulósica presente, predominantemente en fase sólida junto a la lignina. La autohidrólisis de materiales lignocelulósicos produce la fragmentación de estas macromoléculas en compuestos más pequeños como los oligosacáridos y monosacáridos para el caso de hemicelulosas, por ejemplo, el xilano se puede transformar en xilooligosacáridos y estos en xilosas37.
Iones como los hidronios generados por la autoionización del agua, así como la producción de ácido acético producto de la hidrólisis de grupos acetilos sustituyentes presentes en las hemicelulosas, actúan como catalizadores “in-situ”. Estos catalizadores permiten despolimerizar estructuras de bajo peso molecular y monosacáridos53. El aporte de iones H3O+ provenientes del ácido acético es mucho mayor que de la autoionización del agua. A 250 °C y considerando una solubilización del 100% de los grupos acetilo de la biomasa, el aporte de iones H3O+ de estos sustituyentes es 9400 veces mayor que la contribución del agua disociada54.
La autohidrólisis se puede emplear como primera etapa de fraccionamiento de procesos de despolimerización de materiales lignocelulósicos, entendida esta como una disminución de los pesos moleculares de polímeros como la celulosa, hemicelulosa y lignina teniendo como productos oligosacáridos y monómeros. La fracción sólida agotada (rica en celulosa y lignina) pueden ser aprovechados en la obtención de pulpa de celulosa55, azúcares fermentables56 o combustibles57.
Una de las ventajas del proceso de autohidrólisis, es que genera menos corrosión en la maquinaria utilizada y una reducida concentración de inhibidores comparado a los procesos ácidos o alcalinos58. No obstante, pueden ser coadyuvados por agentes químicos como ácido acético59.
Cuando la autohidrólisis es muy intensa, se pueden obtener compuestos como furfural (procedente de la degradación de xilosa), hidroximetilfurfural (procedente de la degradación de manosa, galactosa y glucosa), ácido fórmico y ácido acético (grupos acetilo), que podrían inhibir el proceso de fermentación60.
La rapidez del proceso hidrolítico de la fracción celulósica se incrementa con el aumento de la temperatura de reacción, llegando a una producción de glucosa del 70% a 260 °C. No obstante, reacciones secundarias ocurren a valores por encima de 220 °C, existiendo subproductos difíciles de controlar cuando la temperatura sobrepasa estos valores61. En la Tabla 3 se presenta algunos parámetros y rendimiento del proceso de autohidrólisis para diversa biomasa vegetal.
Hidrólisis ácida
Este tratamiento hace uso de catalizadores ácidos como el sulfuroso, clorhídrico, sulfúrico, fosfórico y nítrico, ya sea en forma concentrada o diluida. La hidrólisis ácida produce la despolimerización de las cadenas de hemicelulosa y celulosa, y su degradación hasta llegar a sus principales monómeros. Soluciones concentradas de ácidos suelen operar a baja temperatura, en tanto que la utilización de ácidos diluidos debe operar a valores cercanos de 240 °C. La granulometría de la partícula (menores a 0.5 mm), y la concentración de la solución ácida influyen en la generación de azúcares reductores a partir de residuos agrarios69. El uso de ácidos concentrados (10-30% p/p) a 170-190 ºC por tiempos prolongados pueden llegar a hidrolizar el 80% de hemicelulosa y el 45% de celulosa70.
El ácido diluido afecta preferentemente a la hemicelulosa, en cambio, presenta un reducido impacto degradativo sobre la lignina71. Para la cáscara de naranja, se ha reportado que la hidrólisis con ácido diluido es una de las mejores opciones para la despolimerización de celulosa y hemicelulosa72. En la Tabla 4 se recogen los parámetros de proceso y generación de azúcares reductores a partir de biomasa vegetal con diferentes ácidos comerciales.
Tabla 4 Parámetros de hidrólisis ácida para la producción de azúcares reductores a partir de biomasa vegetal.
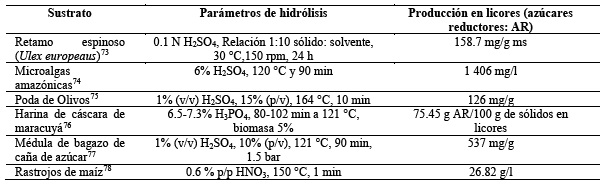
La hidrólisis ácida diluida (1-3% p/p) requiere una alta temperatura (200-240 °C) para romper los cristales de celulosa79. Es seguido por la degradación de hexosas y pentosas y la generación de compuestos tóxicos como hidroximetilfurfural y fenoles perjudiciales para una efectiva sacarificación80.
Los mejores rendimientos para la conversión de celulosa y hemicelulosas en azúcares monoméricos se obtuvieron con una combinación de hidrólisis: una a alta concentración de ácido sulfúrico (alrededor del 70% p/p) a baja temperatura (alrededor de 30 °C), seguida por otro paso a baja concentración de ácido sulfúrico (alrededor del 4% p/p) a alta temperatura (alrededor de 120 °C). Estas condiciones de fraccionamiento produjeron un extracto que contenía todos los azúcares en su forma monomérica, pero también, ácido acético, furanos y compuestos fenólicos81.
Algunos de los problemas con el tratamiento en los casos de la utilización de ácido diluido, se pueden mitigar reemplazando el ácido sulfúrico con ácido fosfórico. Se ha demostrado que cuando se usa ácido fosfórico, la concentración de inhibidores es menor. Además, el ácido fosfórico permite el uso de calidades inferiores de acero inoxidable durante el tratamiento, lo que resulta en una reducción considerable de los costos de capital de inversión en maquinaria para el proceso productivo82.
Hidrólisis alcalina
Las soluciones de álcalis (NaOH, KOH, o NH3) son convenientes para retirar la lignina y aumentar la digestibilidad de la celulosa. También puede realizarse con solventes orgánicos como el etanol o mezclas solvente-agua, en la presencia o ausencia de catalizadores. La hidrólisis alcalina permite a la enzima, acceder con mayor facilidad a la fracción celulósica y hemicelulósica provocando alteraciones morfológicas de sus estructuras macroscópicas como el incremento del área del polímero, así como de su porosidad83.
La fracción acuosa del tratamiento alcalino es de color negro intenso y está constituido de lignina soluble en álcali, estructuras fenólicas derivadas de la degradación de la lignina y hemicelulosa. Debido a su alto pH, estos licores tienen un efecto perjudicial sobre el medio ambiente, especialmente sobre los parámetros DQO y DBO84.
Los tratamientos con álcalis degradan ligeramente los polisacáridos, y en menor medida que los ácidos. Soluciones alcalinas tienen mayor impacto sobre las maderas y pueden eliminar los grupos acetilos de las hemicelulosas85. En condiciones de baja severidad (temperatura, presión y concentración), este método no genera tantos inhibidores en comparación con el tratamiento ácido86.
En condiciones alcalinas, los monómeros fenólicos (principalmente ácido ferúlico y p-cumárico) generan uniones entre las unidades de lignina, y, por otro lado, las hemicelulosas se solubilizan en el caldo de reacción. Las ligninas pueden ser utilizadas como aditivos alimentarios, en productos cosméticos y farmacéuticos debido a su actividad antioxidante, hipocolesterolemiante, prevención de trombosis y aterosclerosis, actividad antimicrobiana y antiinflamatoria, y efecto anticancerígeno87),(88. El ácido ferúlico también se puede utilizar para producir vainillina, mediante transformación microbiana89.
Se ha documentado que la acción combinada de un álcali y un oxidante, como el peróxido de hidrógeno a baja temperatura, puede hidrolizar eficazmente la lignina90 Una concentración del 1 a 2% p/v de H2O2 durante el tratamiento con álcali permitió reducir la concentración de NaOH del 4% al 1%. Esta reducción de álcali es importante ya que, es probable que la concentración excesiva de NaOH provoque la degradación de xilano, disminuya la presencia de xilosa durante la hidrólisis enzimática, y en consecuencia, genere mayores cantidades de licor negro alcalino91.
Cuando los procesos de hidrólisis tanto ácida como alcalina es muy intensa se generan subproductos degradativos como hidroximetilfurfural y furfural, provenientes de hexosas y pentosas respectivamente92.
En la Tabla 5 se muestran los parámetros de proceso y la producción de azúcares reductores a partir de biomasa vegetal con diferentes álcalis comerciales.
Tabla 5 Parámetros de hidrólisis alcalina para la producción de azúcares reductores a partir de biomasa vegetal.
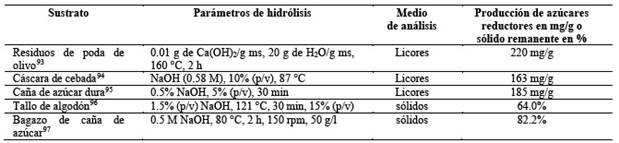
Los tratamientos con bases como el NaOH tienen un mayor impacto en la degradación de lignina que sobre la degradación de hemicelulosa y celulosa. Ante ello, al aplicar NaOH sobre mazorca de maíz permitió determinar una reducción del porcentaje de lignina presente de 22.51 a 9.50%, un incremento de celulosa de 23.58 a 33.32% y de hemicelulosa de 33.34 a 35.03%, antes y después del tratamiento con dicho álcali98. Lo mismo sucedió con el bagazo de sorgo dulce al pasar de 29.34 a 10.88% para la lignina, de 17.75 a 23.8% para la celulosa y de 16.28 a 13.05% para la hemicelulosa. De todos los álcalis, la cal es uno de los más baratos utilizados para este tipo de tratamiento99.
Hidrólisis enzimática
La eficiencia hidrolítica de las enzimas sobre la celulosa está influenciada por las características del sustrato. Por ejemplo, su grado de polimerización y su cristalinidad, la superficie accesible por la celulasa y la presencia de hemicelulosas y lignina en la matriz sólida100. Los procesos enzimáticos son más limpios y energéticamente más eficientes. Se ha considerado una estrategia de etapas basada en la acción de enzimas como las endocelulasas, las cuales, rompen las uniones internas β-(1,4)-glucosídicas. Esto seguido de las exocelulasas que rompen enlaces β-(1,4)-glucosídicos de los polímeros obtenidos por la reacción con las endocelulasas, generando tetrámeros o dímeros. Y posteriormente, la acción de β-glucosidasas generando dos glucosas101),(102.
Se ha reportado que los productos de la hidrólisis de carbohidratos como la celobiosa inhibe tanto a las celobiohidrolasas como las endoglucanasas al unirse al módulo catalítico de la enzima103 y/o de unión a sustratos como los carbohidratos. Por otro lado, la glucosa inhibe principalmente a la β-glucosidasa y, en menor medida, a las celobiohidrolasas y endoglucanasas104. Asimismo, las hemicelulosas solubles pueden inhibir fuertemente la actividad de la celulasa. Se ha evidenciado una reducción de la eficiencia de hidrólisis de celobiohidrolasa I (CBHI, de Thermoascus aurantiacus), celobiohidrolasa II (CBHII, de Trichoderma reesei) y endoglucanasa II (de T. aurantiacus) por acción del xilano de madera de abedul en la hidrólisis enzimática de la paja de trigo, Avicel y nanocelulosa105. Se postula que los xilooligosacáridos de bajo peso molecular presentan mayor grado de inhibición de la enzima α-glucosidasa, que cantidades molares iguales de celobiosa en concentraciones bajas de sólidos106.
Se ha publicado la utilidad de enzimas hidrolíticas con actividad β-glucanasa, xilanasa, celulasa, hemicelulasa, proteasas, lipasas107),(108 y enzimas con actividad ligninolítica como peroxidasas y lacasas109. Por otra parte, se ha reportado que el contenido en lignina en residuos agrarios limita la acción de celulasas, disminuyendo su actividad catalítica110. En tanto, la hidrólisis con alto contenido de sólidos de materiales lignocelulósicos (superiores al 15% p/p) plantea dificultades técnicas relacionadas con la cantidad reducida de agua libre. La suspensión de material fibroso tiene una viscosidad aparente alta que da como resultado una mala mezcla y limitaciones en la transferencia de masa y calor. Esto reduce la eficiencia de las enzimas principalmente en las primeras etapas de la hidrólisis111. En la Tabla 6 se muestran los parámetros de proceso y la producción de azúcares reductores a partir de biomasa vegetal con diferentes enzimas comerciales.
Tabla 6 Parámetros de hidrólisis enzimática para la producción de azúcares reductores a partir de biomasa vegetal.
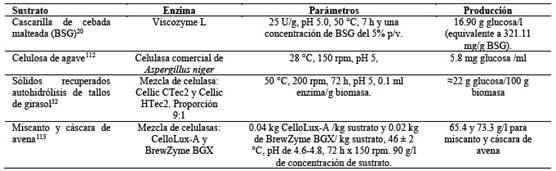
El costo de enzimas como la celulasa es uno de los principales obstáculos que impiden la biorrefinación a gran escala de la biomasa lignocelulósica. Aditivos como el soforolípido y proteína de suero estimulan la hidrólisis enzimática. Cuando la concentración de sustrato fue del 20% (p/v), la presencia de soforolípidos y proteína de suero permitió un aumentó en el rendimiento de glucosa a 17.8% y a 11.9%, respectivamente. Esto podría atribuirse al favor de los soforolípidos para disminuir la adherencia no específica entre sustratos no deseados y enzimas, causada por fuerzas hidrofóbicas y electrostáticas. Además, puede deberse a la capacidad de la proteína de suero para bloquear el sitio de adsorción enzimática de la lignina114.
Tween, polietilenglicol y tensioactivos a base de sulfonato son las formas más importantes de tensioactivos sintetizados químicamente y usados en el proceso de bioconversión de lignocelulosa para disminuir la unión de celulasa-lignina y mejorar el rendimiento de los productos de bioconversión115.
Hidrólisis ácida-alcalina-enzimática
Se ha puesto en evidencia que tratamientos secuenciales conducen a una mayor generación de azúcares reductores, un menor consumo de aditivos químicos, una disminución de los costes de proceso, y una menor generación de subproductos de reacción116. En la Tabla 7 se muestran los parámetros de proceso y la producción de azúcares reductores a partir de biomasa vegetal con diferentes tratamientos combinados de despolimerización.
Tabla 7 Parámetros de despolimerización en tratamientos secuenciales para la producción de azúcares reductores a partir de biomasa vegetal.
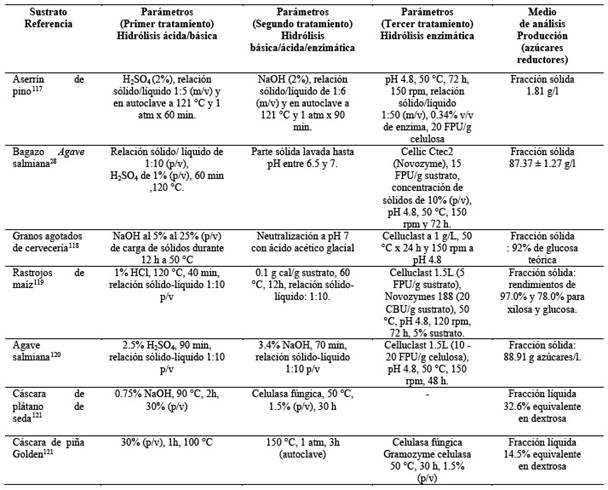
Los tratamientos previos a la hidrólisis enzimática como la alcalinización mejoran los rendimientos de obtención de azúcares reductores. Esto se pone de manifiesto en la alcalinización de mazorca de maíz con NaOH donde incrementó los rendimientos de azúcares reductores de 6.9 a 21.5% utilizando Celluclast 1.5 L y Novozyme 188. La mayoría de los estudios de hidrólisis enzimática en materiales lignocelulósicos se han realizado entre 45 y 55 °C, velocidad de rotación de 100-150 rpm y valores de pH de 4.0 a 5.0 para celulasas y xilanasas, principalmente122.
Una limitante a la acción de la celulasa es la región cristalina de la celulosa, que constituye del 30 al 80 por ciento de la macromolécula, y en la cual, predominan los enlaces de hidrógeno y las interacciones de van der Waals. Cuando la celulasa entra en contacto con la celulosa, inicialmente puede mostrar una mayor acción de endoglucanasa con la región amorfa de la celulosa123.
Otras formas de solubilización de materiales lignocelulósicos
Otras formas de solubilizar la masa vegetal incluyen los tratamientos de expansión de fibra con amoniaco (AFEX), recomendado para material herbáceo y de bajo contenido de lignina. Un inconveniente importante es la baja solubilización de la hemicelulosa, el costo del solvente y su recuperación124. Una de las ventajas es la adición de nutrientes para el crecimiento microbiano a través del amoníaco residual en la biomasa pretratada125. Tratamientos de cáscara de cebada en amoniaco acuoso al 15%, 75 °C durante 48 h, sin agitación, a una relación sólido: líquido de 1:12, permitió rendimientos de solubilización de lignina del 66% y sacarificación del xilano y glucano del 63 y 83%, respectivamente126. La oxidación es otro tratamiento que hace uso de disolventes orgánicos como metanol, etanol, acetona, glicol y etileno. Éste se realiza entre 100 y 200 °C a presión atmosférica. Una gran desventaja es su alto costo e inflamabilidad127. El tratamiento con líquido iónico de la biomasa se caracteriza por sus bajos impactos ambientales. Tiene una mayor incidencia en la hidrólisis de lignina y hemicelulosa. Uno de los líquidos iónicos es la sal de imidazolio, la cual no es volátil, de naturaleza polar, difícil de oxidar, así como fácil de recuperar128.
La ozonólisis es otro tratamiento a la biomasa vegetal, en la cual el ozono reacciona preferentemente con la lignina. Favorece la desestructuración y deslignificación de la biomasa, y por tanto, la liberación de azúcares por hidrólisis enzimática129. La molécula de ozono es muy reactiva hacia compuestos con dobles enlaces conjugados y grupos funcionales con altas densidades de electrones como es la lignina. Genera ácidos como el ácido fórmico y acético que puede resultar en una caída en el pH de 6.5 a 2. Las principales ventajas vinculadas a este proceso son la ausencia de productos de degradación que puedan interferir con la hidrólisis posterior o fermentación y las reacciones que ocurren a temperatura ambiente130.
Esta técnica se ha empleado de forma preliminar en la hidrólisis de la paja de arroz con una dosis de 0.006 gramos de ozono (O3) por gramos de biomasa, y se observó una desintegración del 19% en la cristalinidad de la fibra con una reducción del 17% en el contenido de carbono total131. Asimismo, se evidencia una mejora significativa en el rendimiento de liberación de glucosa en pasto de bermuda costero del 24% al 53% con un consumo de ozono de 26.4 g de ozono por 100 g de biomasa132. También han sido tratadas materias primas como paja de trigo, bagazo, pino, maní, paja de algodón y aserrín de álamo133.
Procesos bajo la técnica de extracción con agua subcrítica permitieron obtener azúcares reductores de la pulpa del fruto de palmera datilera (Phoenix dactylifera). Para ello, la pulpa fue tratada con microondas, teniendo como parámetros óptimos de presión 37.5 bar, temperatura de 130 °C, relación solvente-alimentación de 11 ml/g, y tiempo de 11 minutos. Se recuperó hasta el 8% de azúcares reductores134. Asimismo, se ha empleado el nitrógeno líquido en el tratamiento de biomasas vegetales con fines de sacarificación enzimática. El criotriturado fue altamente eficiente para mejorar la sacarificación del componente holocelulósico de las biomasas vegetales (del 4.3% al 54.1% para aserrín de eucalipto y del 3.9% al 40.6% para cascarilla de arroz). El criotriturado no modificó significativamente los contenidos de celulosa, hemicelulosa y lignina tanto en el aserrín de eucalipto como en la cascarilla de arroz. Sin embargo, por microscopía electrónica se evidenció una desorganización sustancial de los materiales lignocelulósicos135.
Por otra parte, el tratamiento por ultrasonido aplica el principio de cavitación que forma millones de microscópicas burbujas de vapor. La explosión de estas burbujas genera alta temperatura (1700-4700 °C) y presión (1800 bar) en un microsegundo. Esto produce ondas de choque que inducen efectos mecánicos como romper moléculas más grandes en más pequeñas fracciones con reducción de tamaño de partícula136),(137. La aplicación de tratamiento ultrasónico sobre la actividad de celulasas comerciales (Celluclast ® 1.5 L y Cellic ®CTec2) en la hidrólisis de bagazo de caña de azúcar (2% p/v) mejoró la concentración de azúcares reductores en un 89.37% en comparación con el control (muestra no sonificada) (138.
Por otra parte, la aplicación de descargas eléctricas de alto voltaje (HVED) (222 kJ/kg) previa a la hidrólisis enzimática con Viscozyme® L (12 FBGU/g) sobre cáscaras de naranja frescas o desgrasadas permitió la extracción de polifenoles (0.7 g/100 g ms) y azúcares fermentables (50 g/100 g ms) (139.
Purificación de licores de autohidrólisis o hidrólisis ácida y/o alcalina
El refinamiento de licores de autohidrólisis que permitan aumentar la pureza de los oligosacáridos requiere de tratamientos fisicoquímicos individuales o secuenciales (como evaporación, precipitación, extracción, cromatografía, adsorción, intercambio iónico, ultra-nanofiltración o diafiltración140. Dependiendo de la severidad del tratamiento de despolimerización (combinación de tiempo, temperatura, presencia o no de sustancias químicas) se pueden generar inhibidores a la acción enzimática, especialmente aquellos provenientes de los derivados de lignina como el ácido benzoico y el ácido cinámico. Así también, se pueden generar los provenientes de los derivados/sustitutos de los carbohidratos como el ácido acético, ácido fórmico, ácido levulínico, furfural, hidroximetilfurfural, xilooligomeros, glucooligomeros y celobiosa141. En muchos hidrolizados de naturaleza lignocelulósica se presentan compuestos fenólicos los cuales tienen un efecto inhibitorio en los procesos fermentativos, siendo los de menor peso molecular lo más perjudiciales142. La misma actividad inhibitoria lo presenta el ácido 4-hidroxibenzoico, la vainillina y el catecol143.
La evaporación es un procedimiento simple que permite eliminar el ácido acético, el furfural y otros componentes volátiles de los hidrolizados. Sin embargo, esto no ocurre con los monómeros fenólicos y los productos de degradación de lignina144. La concentración de hidrolizado ácido de madera de eucalipto fue cinco veces sometido a evaporación a 70 °C. Este procedimiento condujo a la eliminación del 97.7% de furfural, el 61.3% de ácido acético y el 22.8% de hidroximetilfurfural145. La evaporación en condiciones ácidas (pH 1) favorece la eliminación del ácido acético, que es volátil solo en su forma protonada; sin embargo, las condiciones ácidas fueron menos favorables para la eliminación de hidroximetilfurfural146.
La detoxificación o purificación de los hidrolizados podría lograrse utilizando carbón activado, resinas de adsorción, compuestos alcalinos y enzimas147, o realizando una extracción líquido-líquido con un solvente orgánico. El tratamiento de hidrólisis ácida en la biomasa produce derivados de furano, fenoles y ácidos orgánicos, que son perjudiciales para los microorganismos fermentadores. La eliminación de compuestos inhibidores del hidrolizado mediante la adsorción de carbón activado con cáscara de coco es esencial para mejorar la calidad del hidrolizado desintoxicado como materia prima para la producción de xilitol148. La extracción líquido-líquido presenta algunos beneficios en comparación con los otros métodos de purificación ya que permite la remoción de los compuestos tóxicos sin pérdida de carbohidratos y permite la recuperación del solvente149.
Se aplicaron resinas comerciales como la XAD4, XAD16HP, XAD7HP utilizadas para la recuperación de compuestos fenólicos de hidrolizados de cáscara de melón150. Asimismo, la resina de poliestireno divinilbenceno (PS-DVB) se usó como material de adsorción para eliminar simultáneamente los inhibidores de la fermentación de licores de madera dura151. Asimismo, se evaluó la separación y purificación simultánea de lignosulfonato y xilooligosacáridos (XOS) del licor gastado de paja de trigo con un tratamiento de bisulfito de magnesio. Una columna de lecho fijo con la resina D354 permitió una recuperación del 93.09% de XOS y del 98.03% de lignosulfonato152. En otros trabajos153 la remoción de lignina siguió una combinación de cloruro de polialuminio, carbón activado y resina XAD-4 para tratar los licores de la hidrólisis de madera de álamo. Cuando el pH del medio se ajusta a 5.5, las resinas de intercambio aniónico presentan la mejor eliminación de inhibidores de fermentación154. En tanto un pH de 10 aumentó la adsorción de ácidos carboxílicos alifáticos, así como derivados de furano155.
La ultrafiltración es un enfoque eficaz para la separación y purificación de componentes orgánicos disueltos en licor de prehidrólisis de materiales lignocelulósicos156 . Se pueden usar membranas con cut off de 10 a 50 kDa para separar la lignina o las proteínas presentes en el líquido retenido, de los azúcares monoméricos, el ácido sulfúrico, el ácido acético y los furanos presentes en el líquido permeado a través de la membrana157. Membranas con 150-300 Da pueden retener glucosa, xilosa y arabinosa, mientras que el ácido acético y los furanos atraviesan las membranas158. Membranas de lámina plana de 10, 20 y 50 kDa permitieron retener macromoléculas de lignina y proteínas de un hidrolizado ácido de salvado de trigo, a diferencia de las membranas tubulares cerámicas con menor cut off (8 y 15 kDa), donde la retención de macromoléculas fue menor159. La filtración de hidrolizado ácido diluido de paja de arroz ajustado a pH 3 en una membrana orgánica enrollada en espiral con un cut off de 150-300 Da condujo a una retención total de glucosa, y una retención muy alta de xilosa y arabinosa (más del 94%). En cambio, el ácido acético y los furanos atravesaron totalmente la membrana. El rendimiento de separación disminuyó cuando la temperatura de operación se incrementó de 25 a 40 °C157.
Membranas de nanofiltración con tamaño de poro de 120 Da han permitido separar compuestos fenólicos producto de la despolimerización de la matriz lignocelulósica con una eficiencia del 99%. El ácido benzoico (PM 122 Da) es el fenol más pequeño lo que significa que todos los compuestos fenólicos deben ser retenidos por membranas de 120 Da160. Asimismo, se emplearon los licores de tallos de quinua (Chenopodium quinoa) (QS) sometidos a autohidrólisis (178 °C y 10 bar) e hidrolisis enzimática para la producción de xilooligosacáridos (79 mg XOS /g de biomasa). Se produjo mayormente xilotetraosa (X4) a xilohexaosa (X6) en 20 min de proceso, mientras se evidenció un mayor contenido de xilobiosa (X2, 18 mg/g de QS) y xilotriosa (X3, con contenidos de 18 mg/g de QS) en 45 min. Se sometieron a ultrafiltración con una membrana de 10 kDa, observándose un mayor flujo de permeado a pH 6,6 que a valores de pH más bajos (3.6, 4.6 y 5.6). En el retenido después de la nanofiltración-NF (150-300 Da), se recuperó el 56% del total de XOS (X2-X6) (161.
Estrategias combinadas implican el uso de carbón activo (1 g/l), separación por membranas (poliester sulfona de 1000 Da, 7.25 kPa, pH 4) y adsorción por resinas de intercambio aniónico (A-IRN78), especialmente en los hidrolizados de mazorca de maíz (0.5% HNO3, 121 °C, 30 min), para la obtención de xilitol por rutas biotecnológicas (Candida tropicalis, MTCC 6192, pH 4.5, 48 h, 150 rpm a 30 °C) (162.
Determinación de azúcares reductores
El método DNS constituye una reducción del ácido 3,5-dinitrosalicílico por acción del calor, y de los azúcares reductores. De esta manera permite determinar la presencia de grupos carbonilos libres (C=O) perteneciente a los azúcares reductores. Su determinación se realiza por espectrofotometría-colorimetría a 540 nm y utilizando como patrón, 2 g/l de glucosa con sus respectivas diluciones. Bajo este método se han cuantificado azúcares reductores a partir de la hidrólisis ácida de la harina de la cáscara de Manihot esculenta (yuca) (163. Sin embargo, este método no es aconsejable cuando los azúcares reductores se encuentran en presencia de furanos, ya que puede generar una sobre estimación de azúcares reductores hasta en un 68%. Incluso la presencia de furfural y 5-HMF conduce a una sobreestimación de estos valores164.
El método Eynon-Lane se basa en la reacción de un medio básico de alta concentración que requiere un estabilizador para el ión Cu+2 como el tartrato, para evitar la formación de Cu(OH)2 insoluble. No brinda exactitud en la cuantificación de azúcares reductores en melaza de caña debido a la presencia de especies inorgánicas y moléculas con grupos aldehídos. La exactitud puede disminuir también por la presencia de cetosas que pueden sufrir efectos de tautomerización, otorgando valores mayores a los reales165. Mediante esta técnica se determinaron los azúcares reductores del hidrolizado de bagazo de sorgo dulce166, así como del hidrolizado enzimático de la cáscara de plátano119 y de piña167.
El método de cromatografía líquida de alta resolución (HPLC) brinda mayor precisión en la cuantificación en azúcares reductores que el método de Eynon-Lane, especialmente en la caracterización de melaza de caña163. Columnas como Aminex HPX-87H (BioRad Life Science Group, Hercules, CA, USA a 50 °C, fase móvil de H2SO4 0.003 N a 0.6 ml/min33), y columna como la CarboPac PA20 de elución isocrática con 10 mM NaOH a un caudal de 0.5 ml/min con un paso de regeneración de columna utilizando NaOH 200 mM a 0.5 ml/min116 han sido reportadas para la determinación de este tipo de elementos. Así mismo, columnas como BioRad Aminex HPX-87P (80 °C con flujo de 0.6 ml/min de agua milli-Q)43, Shodex NH2P-50 4E (acetonitrilo 80%, 1 cm3/min) (168, Shodex SP 0810 (85 °C, agua ionizada 0.6 ml/min)117, Agilent HiPlex H (60 °C con 5 mM H2SO4 de fase móvil y flujo de 0.7 ml/min160 han permitido la cuantificación de monómeros y oligosacáridos hidrolizados.
El método Fehlig Causse Bonnans es empleado para determinar azúcares reductores en mostos y vinos previo proceso de decoloración con carbón activado y acetato de plomo. Se basa en el mismo principio que el método de Eynon-Lane, el cual, es la reacción de los azúcares reductores con el cobre en medio alcalino6. Esta metodología ha sido aplicada para determinar azúcares reductores en diversas especies de zanahoria169. El método de Folin-Wu se fundamenta en que los aldehídos (glucosa) se oxidan a ácidos y el cobre del tartrato cupro alcalino se reduce a (Cu2O) oxido cuproso. Este método fue usado en la cuantificación de azúcares reductores en la fermentación de brácteas de alcachofa para producir biomasa de Candida utilis var. major CECT 1430170, así como en la obtención de azúcares reductores proveniente de planta seca y fraccionada de maíz amarillo duro después de realizar la hidrólisis mixta como resultado de la combinación del método físico y físico-químico171.
La metodología Nelson-Somogyi cuantifica los azúcares reductores y no reductores, especialmente en concentraciones de 20-180 mg/l172. Este método es mucho más preciso en la cuantificación de azúcares reductores en miel de abeja que los métodos Luff-School y Munson-Walker que presentan valores más bajos173. El ensayo DNS es aproximadamente 10 veces menos sensible que el ensayo Nelson-Somogyi y no proporciona datos estequiométricos con oligosacáridos. Esto ofrece valores significativamente más altos de azúcares reductores que el número real de grupos reductores hemiacetal174. DNS ha sido recomendado por la comisión de biotecnología de la IUPAC para medir las actividades estándar de celulasa contra papel de filtro y carboximetilcelulosa (CMC) (175. Por otra parte, el método DNS presenta mayor coeficiente de correlación que el de Eynon-Lane especialmente para zumos de caña de azúcar176.
Aprovechamiento de los azúcares reductores
Existe una diversa gama de azúcares reductores (glucosa, xilosa, arabinosa, maltosa, maltotriosa, maltopentosa y dextrinas, entre otros) (177. Los azúcares de bajo peso molecular provenientes de la celulosa y hemicelulosa son favorables para la generación de biocombustibles178, mientras que las hemicelulosas con un alto peso molecular pueden usarse en cosméticos y productos farmacéuticos179. La transformación de los materiales lignocelulósicos a alcohol etílico requiere de la eliminación de la lignina para generar celulosa del complejo celulosa-hemicelulosa-lignina y poder producir monómeros de hexosas y pentosas115.
Se ha reportado la sacarificación de las cascarillas de maíz, maní y café por enzimas lignocelulolíticas secretadas por Sphingobacterium sp. ksn para la producción de bioetanol180. Otras materias primas como bagazo de caña181 también han sido aprovechadas para obtener etanol. Levaduras como Clavispora lusitaniae CDBB-L-2031, han sido empleadas para producir etanol y xilitol debido a su capacidad para asimilar xilosa, celobiosa y glucosa182. También han sido reportado estudios relacionados con la utilización de levaduras como Pichia stipitis, Debaryomyces hansenii o Candida shehetae en la fermentación de medios que contienen xilosa derivados de materiales lignocelulósicos183),(184),(185.
El ácido levulínico se puede extraer por deshidratación de azúcares, hidratación de hidroximetilfurfural (HMF) o hidrólisis de alcohol furfurílico, ambos derivados de la xilosa, que es un azúcar de la hemicelulosa186. Puede obtenerse por hidrólisis ácida con 1% HCl, 160 °C y 3 h a partir de cáscara de arroz y tallos de maíz187. También puede obtenerse con H2SO4 al 5%, 200-240 °C entre 2-4 h para madera de álamo, pino y abeto188 o con bagazo de caña189. El ácido levulínico tiene aplicaciones en las industrias de aditivos, farmacéutica y plástica190.
El ácido succínico puede obtenerse de fracciones hemicelulósicas ricas en xilosa como las provenientes de semillas de aceituna y bagazo de caña de azúcar191, bagazo de agave192 y melaza de caña193 por acción de Actinobacillus succinogenes. Parámetros de 0.07-0.7% H2SO4, 180 °C por 8 min en madera triturada de pino194 y de 2-6.5 g/l Na2CO3, 185-195 °C por 10-15 min sobre paja de trigo195 fueron reportados para la obtención de este tipo de metabolitos.
El xilitol, un alcohol de cinco carbonos, se usa ampliamente como sustituto del azúcar en la industria alimentaria por su similitud en dulzura a la sacarosa. No requiere de insulina, previene la caries dental y es bajo en calorías196. Ensayos para su producción se evidencian a partir de hidrolizado hemicelulósico de paja de colza197, hojas de plátano198, hojas de palma aceitera146, cáscara de arroz199. Se han hecho uso de hidrolizados ricos en xilosa obtenidos en reacción de H2SO4 al 1% v/v, 121 °C durante 30-60 min y utilizando cepas como Candida tropicalis, Candida magnoliae, y Candida guilliermondii200),(201),(202.
El ácido láctico es un aditivo obtenido de residuos lignocelulósicos mediante ruta microbiológica. Se han hecho uso de Lactobacillus brevis, pentosus ATCC 8041, rhamnosus, L. rhamnosus ATCC 9595 (CET288) entre otros203),(204),(205),(206. Se ha reportado que cáscaras de piña constituye una fuente promisoria para la obtención de ácido láctico mediante la acción de Lactobacillus acidophilus207, así como los hidrolizados de maíz son fuente de hexosas y pentosas por la acción de Bacillus coagulans IPE22208.
Por otra parte, se han utilizado cáscaras de naranja y plátano sin ningún tratamiento previo para la producción de biohidrógeno. Este producto se obtiene por fermentación oscura (40 °C x 4 días, 120 rpm) con Clostridium beijenrickii, llegando a rendimientos superiores a 86 ml de H2 desplazado, por gramo de azúcar reductor alimentado209. Asimismo, se evaluó el efecto de la concentración de AR y extracto de levadura en la obtención de hidroxibutirato (PHB, bioplástico) por Bacillus sp B23 a partir de hidrolizado de granos y levadura cervecera residual. La carga inicial recomendable de AR y extracto de levadura óptimas para la producción de PHB fueron 34.14 g/l y 4.41 g/l, respectivamente. Bajo estos parámetros se acumuló el 55% de PHB en biomasa y una ratio productiva de 0.1245 g/l.h en 24 horas210. Por otra parte, se ha empleado azúcares reductores proveniente de brácteas de alcachofa para la generación de levadura Candida utilis var. major. CECT 1430 con propósitos de obtener proteína celular168.
CONCLUSIONES
La composición química de las materias primas depende de la variedad de su especie vegetal, las condiciones del cultivo y el grado de madurez de la planta. Estas variables generan una variación en su composición y el comportamiento del sustrato frente a una reacción de hidrólisis. El acceso a la estructura de la matriz lignocelulósica constituye un reto. Los factores que afectan la solubilización de estas macromoléculas incluyen su grado de polimerización, hidrofobicidad, cristalinidad, área superficial, entre las más importantes.
Estructuras como la lignina y la pectina obstaculizan la hidrólisis de la celulosa y hemicelulosa. Por tanto, es necesario un tratamiento adecuado de deslignificación de la biomasa para lograr la máxima hidrólisis de la celulosa, que es un requisito previo para la fermentación eficaz de los azúcares liberados para la producción de etanol.
Los principales tipos de tratamientos incluyen el físico, químico y biológico, de los cuales se privilegia el biológico por sus ventajas de condiciones suaves, no contaminantes y de bajo consumo energético. Sin embargo, los tratamientos con ácidos y álcalis son mayormente utilizados por su mayor rendimiento de azúcares reductores en comparación a los biológicos o enzimáticos.
A partir de los aspectos más destacados y desafíos de los métodos de tratamientos discutidos, se puede observar que, aunque un único tratamiento hace una contribución significativa, ningún método por sí solo proporciona resultados eficientes debido a sus limitaciones intrínsecas. Por lo tanto, las estrategias combinadas de tratamientos podrían reducir estas desventajas y brindar un resultado deseado. El principal desafío para el aprovechamiento de la biomasa es el diseño eficiente, económico y sostenible del tratamiento (físico o químico) para romper y abrir la estructura lignocelulósica compleja. Un segundo desafío se centra en, las estrategias de purificación de metabolitos de inhibición que limitan la eficiencia del proceso y así, facilitan el acceso de las enzimas durante la hidrólisis. Consecuentemente se produce un incremento en la velocidad y el rendimiento de la liberación de azúcares.
Para futuras investigaciones quedan vacíos relacionadas con el análisis técnico-económico y la eficiencia energética de los diversos tratamientos y sus combinaciones respectivas.