INTRODUCCIÓN
El carbón activado es un material poroso que permite la adsorción de diferentes materiales. Uno de sus usos más comunes es la remoción de contaminantes existentes en medios acuosos y/o gaseosos. Sus diversos usos lo convierten en un valioso producto. De manera común, el carbón activado es obtenido a partir de carbón mineral. Este último es activado mediante diferentes procesos ya sean estos físicos o químicos. El carbón activado es muy apreciado por su versatilidad de usos y es ampliamente utilizado como un agente de remoción de contaminantes acuosos y gaseosos. Se utiliza en filtros de agua como agente adsorbente de componentes de peso molecular entre 17g/mol (cloro) y 82g/mol (plomo) para conseguir la potabilización de ésta. Por otro lado, permite la remoción de compuestos orgánicos volátiles (COVs) de flujos gaseosos. Por ejemplo, permite la remoción del sulfuro de hidrógeno en plantas de biogás. Las aplicaciones que tiene el carbón activado son la recuperación de solventes, colorantes, y la eliminación de contaminantes orgánicos y compuestos mercúricos en la industria química. También, es usado en la industria alimentaria como agente de remoción de compuestos aromáticos policíclicos (PAHs), la purificación de aditivos, la eliminación de óxidos e impurezas, y en el refinamiento del sabor y el olor en bebidas. Como finalidad de este estudio se busca determinar las mejores condiciones de operación para la obtención de un carbón activado de gran área superficial específica a partir de mezclas de plásticos de deshecho mediante un proceso pirolítico.
Los procesos pirolíticos corresponden a una clasificación de procesos termoquímicos de transformación. Se caracterizan principalmente por llevar a cabo la degradación térmica de las cadenas poliméricas que constituyen la materia prima. En el caso de PET nos referimos a las cadenas de tereftalato de polietileno los cuales se degradan a temperaturas entre 300 a 600°C en ausencia de oxígeno. La distribución de productos obtenidos, a partir de plásticos, en este tipo de procesos son normalmente gases y ceras, dejando una pequeña cantidad de carbón residual menor al 20%. Cuando un plástico es sometido a un tratamiento termoquímico, sufre una degradación rápida y poco controlable. Para poder controlar la cantidad de material generado, y aumentar el área superficial específica que el material carbonoso posee, se puede aplicar un pretratamiento de activación. Este, convierte el material carbonoso en carbón activado. Una vez obtenido el material, éste debe ser lavado para remover trazas del agente de activación. Luego, debe ser neutralizado para su caracterización y posterior aplicación. Este proceso es beneficioso ya que permite la transformación de un material de desecho en un material valioso que coadyuve a la remoción de contaminantes gaseosos y acuosos.
En el presente estudio, se realizó la activación mediante la impregnación de la mezcla de plásticos con H3PO4. Se realizaron estudios mediante TGA, y DSC. En seguida, se determinó el área superficial específica aplicando una fisisorción de nitrógeno gaseoso en la superficie del material y aplicando el método de Single Point BET.
RESULTADOS Y DISCUSIONES
Rango de temperaturas de pirólisis sin pretratamiento de PET
Para la determinación del rango de temperaturas a estudiarse en la pirólisis de PET, se obtuvieron datos de la degradación térmica de PET sin pretratamiento. El termograma obtenido se muestra a continuación en la Figura 1.
Como se puede observar en la Figura 1, la pérdida de masa empieza a los 350°C y termina aproximadamente a los 650°C. Existe una fluctuación en el flujo de calor entre los 400°C y 450°C que indica la existencia de un proceso de transformación en este rango. Por esta razón, se puede considerar que la reacción de degradación térmica concluye a los 450°C. Ésta es la temperatura mínima necesaria para no interrumpir las reacciones de transformación que se dan durante la degradación térmica. A temperaturas menores es posible que no todo el material se degrade térmicamente produciendo reacciones secundarias partiendo del PET a Gas - Vapor - Carbón. Esto puede implicar la formación de grupos funcionales o productos no deseados, y así mismo, la obtención de productos no totalmente carbonosos. Como se puede observar en la gráfica, la reacción de degradación térmica del material toma relativamente poco tiempo (aproximadamente unos 10 minutos). Sin embargo, una vez que la temperatura de degradación térmica es alcanzada esto no implica el fin de la reacción pirolítica. Posteriormente a alcanzar la temperatura tope del proceso, se producen reacciones secundarias entre los gases, compuestos volátiles y carbón. Estas reacciones secundarias definen algunas características fisicoquímicas del producto como ser el tipo y la cantidad de grupos funcionales presentes en la superficie del carbón, el rendimiento másico, el área superficial específica, y la capacidad de intercambio catiónico, entre otros. El tiempo en el que estas reacciones secundarias se producen no es indeterminado, y las propiedades expuestas anteriormente no varían de forma lineal respecto al tiempo. En este sentido, este tiempo de reacción posterior a la temperatura tope es determinado de manera experimental.
Rango de temperaturas de pirólisis con pretratamiento de PET
Por otro lado, se estudió la degradación térmica de PET pretratado con H3PO4. El diagrama TGA y DSC se muestra a continuación en la Figura 2.
Se puede observar que el pretratamiento con H3PO4 produce una expansión en el tiempo que le toma al material degradarse. Bajo estas condiciones, el PET es más estable durante el tratamiento térmico y permite la recuperación de mayores cantidades de sólido (carbón activado). Se puede observar también que, las transformaciones, indicadas por el cese de oscilaciones en la curva de flujo de temperatura (DCS), son preponderantes hasta antes de los 450°C. Posterior a este punto, el comportamiento de la curva DCS presenta un comportamiento quasi-lineal, lo cual, señala que no existen cambios de estado en esa región térmica. Se puede inferir de esto que las reacciones principales de degradación se terminan en este punto. Esto concuerda con la disminución en la tasa de disminución del porcentaje másico del material. Sin embargo, se puede observar que existe una segunda etapa de degradación térmica posterior a los 450°C, y esta puede ser atribuida a la acción del agente de activación, el cual, produce reacciones adicionales durante la degradación térmica. Por referencia, se sabe que durante la degradación térmica de PET entre los 300 y 400°C se producen principalmente acetaldehídos, monóxido y dióxido de carbono. Posteriormente, se generan otros compuestos en menor proporción como ser alifáticos de C1 hasta C4, bencenos y benzoato de vinilo entre otros 1. Sin embargo, en el caso de la reacción previo tratamiento con H3PO4, el mecanismo de reacción que produce estos materiales es afectado por el agente de activación, produciendo compuestos adicionales no determinados durante este estudio. De lo anterior podemos inferir que una forma de conocer la temperatura máxima a la cual se producen las transformaciones en el proceso, es mediante la curva DSC. Por tanto, se utilizó este método para delimitar la temperatura mínima a la que las reacciones de degradación principales son llevadas a cabo, en este caso 450°C. Por otra parte, la temperatura máxima de experimentación fue establecida como 600°C. Por referencia, sabemos que el carbón activado puede ser producido hasta los 800°C2. Sin embargo, se optó por los 600°C por una razón primordial, el material de nuestro reactor (tubo de boro silicato) sufre degradaciones a temperaturas superiores a los 600°C, impidiendo así que se hicieran pruebas a temperaturas superiores sin afectar la integridad de los productos obtenidos. Como aclaración, la reacción que ocurre a los 600°C está compuesta por reacciones secundarias entre los materiales volátiles y el material carbonoso. Estas reacciones y mecanismos de reacción, no han sido determinados para reacciones que involucren H3PO4. Por otro lado, las reacciones secundarias que se dan entre los volátiles y la fase sólida son las que otorgan las propiedades fisicoquímicas y grupos funcionales a la superficie del carbón activado. Además, la temperatura a la que el proceso se lleva a cabo determina el tipo de compuestos volátiles que serán capaces de reaccionar, dando así, diferentes características al carbón activado resultante3.
Proceso pirolítico
En base a los estudios calorimétricos, el proceso pirolítico fue llevado a cabo con un tratamiento previo de impregnación del PET con ácido fosfórico. Los estudios de pirólisis estuvieron acorde al siguiente diseño experimental, mostrado en la Tabla 1.
Respuesta Área Superficial Específica
Se realizó un análisis ANOVA de acuerdo al diseño mostrado en la Tabla 2 (Sección Experimental) y en la Tabla 1. Se pudo determinar que los factores significativos para la respuesta área superficial específica son principalmente la temperatura del proceso y el tiempo de pirolisis. Los estadísticos obtenidos para estos factores fueron p-values de 0.096 y 0.036, respectivamente; y F-values de 4.18 y 8.11, respectivamente. El factor relación en peso de la impregnación fue determinado como estadísticamente no significativo en vista que el valor de la probabilidad fue de 0.764, el cual, es mucho mayor a 0.05 (límite de significancia para este parámetro) para un F-value de 0.1. Dicho esto, y acorde a los gráficos de interacción obtenidos (Figura 3), consideramos que el efecto que tiene el factor relación en peso de la impregnación debe ser considerado dentro del modelo estadístico determinado para la variable respuesta área superficial específica. En consideración con lo anteriormente expuesto, podemos decir que una mayor relación en peso de la impregnación significa una mayor área superficial específica. Esto concuerda con lo reportado en otros estudios4.
Se pudo determinar que el modelo presenta un R2 de 0.76 y, es un modelo adecuado para navegar en el espacio del diseño experimental. Los coeficientes del modelo empírico estadístico para determinar el área superficial del producto son los siguientes:
Donde AS es el área superficial específica, T es la temperatura de proceso, tp es el tiempo de pirólisis y TI es la relación en peso de la impregnación. En base al análisis ANOVA se pudo determinar los efectos que tiene cada factor en el espacio experimental que se muestra en la Figura 3.
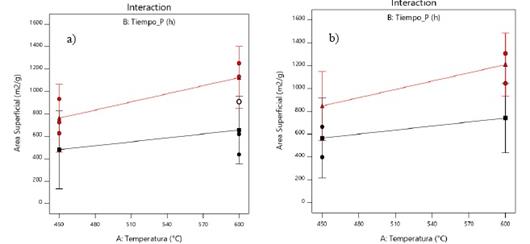
Figura 3 Gráficas de interacciones entre los factores de diseño radio de impregnación y temperatura (°C) y la variable de respuesta, área superficial específica: a) Radio de impregnación 1:1 de wH3PO4/wPET con medias cercanas a los 400m2/g y 700m2/g. b) Radio de impregnación 1:4 de wH3PO4/wPET con medias cercanas a los 600m2/g y 800m2/g.
La Figura 3 contiene gráficas con las interacciones de los factores área superficial (m2/g) y temperatura (°C). La primera (a) muestra el comportamiento a un radio de impregnación 1:1. La línea negra representa el nivel bajo de tiempo correspondiente a 1 hora y, la línea roja representa el nivel alto de tiempo, en este caso 4 horas. Los valores extremos de estas líneas presentan valores promedio con sus respectivas barras de error (desviaciones estándar) a las temperaturas correspondientes de pirólisis. Al lado izquierdo tenemos la mínima temperatura utilizada, correspondiente a 450°C. En el lado derecho, se presenta los valores obtenidos al nivel alto del factor Temperatura, es decir 600°C. Esta interpretación es análoga también a la gráfica (b), la cual, corresponde al nivel alto de radio de impregnación de 1:4. El eje “y” de ambas gráficas corresponde a la variable respuesta, es decir, el área superficial específica.
Se puede observar que la temperatura incide positivamente en el área superficial, siendo el tiempo un factor determinante para la magnitud de este efecto. Se puede observar en la Figura 4 que la relación en peso de la impregnación mejora la media de las áreas superficiales en las diferentes condiciones.
La superficie de respuesta y la gráfica de contornos determinados por el modelo se muestran en la Figura 4, en la que se puede observar la presencia de una curvatura en la superficie de respuesta indicando la proximidad a un máximo. Mediante una aproximación numérica para determinar las mejores condiciones de operación para obtener el mayor área superficial se determinó que a 600°C, 4 horas de operación y un radio de impregnacion de 1:1, se esperaría obtener un área superficial de 1123 m2/g.
Estos resultados fueron corroborados de manera experimental, y se logró obtener áreas superficiales, en las mejores condiciones de operación, entre 1100 a 1250 m2/g.
Respuesta Rendimiento másico
En cuanto a la respuesta rendimiento másico, se realizó un análisis ANOVA de la misma manera que en la respuesta área superficial específica. Se determinó que los factores estadísticamente significativos son la temperatura y la relación en peso de la impregnación, con p-values de 0.11 y 0.05, y F-values de 3.53 y 5.91, respectivamente. Se pudo determinar que los efectos que presentan los factores en el rendimiento másico del material son los presentados en la figura 5.

Figura 4 Gráficas de la respuesta Área Superficial específica del diseño experimental: a) Superficie de contorno, b) Superficie de respuesta.
Se puede observar que, en el caso del rendimiento, existe un efecto negativo causado por la temperatura del proceso. De la misma manera, la relación en peso de la impregnación es un factor con efecto negativo, el cual, operando en la temperatura mínima, reduce el rendimiento másico de una media de 30% a una media del 25% aproximadamente. El análisis ANOVA realizado mostró que no existe un efecto en la variable respuesta rendimiento másico causado por el tiempo en el que se lleva a cabo el proceso. Por tanto, para la obtención de la superficie de respuesta (Figura 6) y el modelo estadístico solo consideraremos los factores temperatura del proceso y relación en peso de la impregnación. La gráfica de superficie de respuesta para el rendimiento másico (Figura 6) muestra que existe un comportamiento lineal del modelo en el rango experimental establecido. Se puede observar que al tener un comportamiento lineal no se evidencia la existencia de un punto de inflexión (máximo) o una curvatura en la superficie de respuesta (comportamiento cuadrático del modelo). A partir de esto se puede inferir que fuera del rango experimental es posible encontrar un punto máximo en la respuesta rendimiento.
El modelo estadístico obtenido mediante el análisis ANOVA es el siguiente:
Así, se puede observar que, probablemente, exista un posible máximo de rendimiento másico a temperaturas menores a 450°C y tasas de impregnación menores a 1:1.
Mediante la determinación del valor de la función de deseabilidad en el modelo estadístico obtenido se pudo estimar el mejor valor posible de rendimiento másico en el rango experimental. Se determinó que a 450°C y 4 horas de proceso y una relación en peso de la impregnación de 1:1, se espera un rendimiento de aproximadamente el 30.9% de masa de carbón activado recuperado y lavado respecto a la masa inicial de PET sin tratar.
EXPERIMENTAL
Determinación del rango de temperaturas para el estudio
Para poder determinar los rangos de temperatura adecuados para la obtención de la mayor cantidad de carbón procedente de la reacción pirolítica, se empleó un análizador termogravimétrico (TGA) y calorímetro diferencial de barrido (DSC) de la marca SETARAM modelo TG DTA - DSC 1600, para las muestras de PET con y sin pretratamiento de activación5), (6.
Metodología del análisis termogravimétrico
Para la aplicación del método termogravimétrico se pesaron 40mg de muestra, la cual, se introdujo en el porta-muestras del equipo. Posteriormente, se programó un calentamiento a tasa de calentamiento constante de 10 °C/min desde 20°C hasta 900°C. En estas condiciones se obtuvo el termograma de degradación térmica del material, todo esto, en una atmósfera de nitrógeno. Se registraron datos de masa y cambios de capacidad calorífica registradas por el equipo. Mediante estos datos, se pudo identificar las temperaturas donde existen cambios de estado en el material. De esta manera, y en conjunto con ambos conjuntos de datos, se pudo determinar la temperatura donde inicia la degradación térmica del material y la temperatura a la que esta degradación termina.
Planteamiento del Diseño Experimental
El diseño experimental establecido para este estudio fue un diseño factorial fraccionado 23-1 donde cada experimento fue realizado por triplicado. En este diseño, los factores elegidos como independientes fueron la temperatura de proceso (T), el tiempo de pirólisis (tp) y la relación en peso de la impregnación (TI). Éstos fueron elegidos en base a las referencias consultadas2),(7. Concretamente, se eligió el siguiente rango experimental:
Pretratamiento con ácido fosfórico
Botellas vacías de material PET recolectadas de gaseosa y agua de diferente procedencia y diferente grado de envejecimiento fueron cortadas de manera manual en partículas de 2mm x 2mm. Este material fue mezclado para asegurar una homogeneidad en las muestras a someterse al tratamiento térmico. La mezcla de PET fue pretratada mezclando relaciones másicas predefinidas de PET y H3PO4 (al 37% v/v) en un volumen de 200ml y enrazado con agua destilada. Para este fin, se puso la mezcla mencionada anteriormente (Tabla 2) en agitación constante en un shaker AGIMATIC - S 7000242 de la marca J.P. SELECTA s.a., a 60°C durante 12 horas. Posteriormente a la impregnación, se procedió a un secado en una mufla eléctrica modelo E28 de la marca BINDER por 24 horas a 105°C7.
Proceso pirolítico
El proceso pirolítico escogido fue llevado a cabo en dos reactores tubulares tipo batch. Ambos reactores difieren en el volumen del reactor y, por tanto, en el flujo suministrado. Al primer reactor se le suministró un flujo constante de 100 ml/min de gas inerte de Nitrógeno. Se suministró energía acorde a una rampa de calentamiento de 10 K/min mediante un horno eléctrico adecuado de un proceso de craqueo catalítico elaborado en el centro de investigación y controlado por un controlador de marca Omron. El segundo reactor de marca Cheng Yi modelo CHY - 1200 fue alimentado con Argón como gas inerte, el cual, fue suministrado a una tasa de 1 L/min con una rampa de calentamiento de 10 K/min. Ambos cilindros de gas fueron adquiridos de la empresa RED - OX y cuentan con purezas de 5.0 en el caso del nitrógeno y 99.999% en el caso del argón. Los reactores utilizados son reactores tubulares del tipo flujo pistón (PFR) que consisten en un horno eléctrico y en su interior de un tubo reactor de cuarzo. A este último tubo se suministra el gas carrier para llevar a cabo la reacción. Ambos reactores fueron reportados en un estudio anterior8.
Determinación del área superficial específica mediante fisisorción de nitrógeno
La determinación del área superficial específica del carbón obtenido fue llevada a cabo mediante una fisisorción de nitrógeno en la superficie del material. Para esto, se empleó el método de Single Point BET mediante el uso de un equipo Chem - BET modelo CBT - 1 de la marca Quantachrome Instrument. Éste cuenta con un error de método del 2%9. El método consiste en la lectura de la señal producida tanto por la adsorción y por la desorción de nitrógeno en la muestra. Estas señales fueron inducidas de manera externa mediante cambios bruscos de temperatura, mediante la inmersión de la muestra en nitrógeno líquido (de la marca RED - OX) (adsorción) y la posterior inmersión de la muestra en agua a temperatura ambiente (desorción). La señal de desorción producida es comparada con la señal producida por inyecciones de nitrógeno gaseoso de un volumen conocido. Una vez que la semejanza entre señal producida y señal alcanzada es satisfactoria, se realiza una comparación numérica de las áreas producidas por las señales. Luego, se determina el volumen adsorbido por la muestra para posteriormente determinar el área superficial mediante el método de Single Point BET.
CONCLUSIÓN
Se logró obtener carbón activado de gran área superficial (1100 a 1250 m2/g) y rendimientos estables (entre 25 y 30% w/w) a partir de mezclas de PET mediante un proceso pirolítico a escala de laboratorio. Esto, bajo las condiciones climáticas de presión de la ciudad de La Paz, Bolivia, donde la presión atmosférica es de 495 mmHg y la temperatura media es de 15°C. Se ha reportado que un decremento en la presión atmosférica reduce el rendimiento de material sólido producto de la pirólisis10. A partir de los experimentos realizados se logró determinar que los factores con significancia estadística para la respuesta área superficial específica son la temperatura, y el tiempo del proceso, y en menor medida, la relación en peso de la impregnación de agente de activación. El efecto de todas estas variables es positivo incrementando el área superficial con el aumento del valor de dichos factores. En el caso de la respuesta rendimiento másico, también se determinaron los factores estadísticamente más significativos. Éstos fueron la temperatura del proceso y la relación en peso de la impregnación de agente de activación. En este caso, el efecto de la temperatura y la relación en peso de la impregnación son negativos. Es decir que cuando aumentan se reduce el rendimiento másico. Gracias a esto se pudo obtener modelos estadísticos para cada variable respuesta.
Gracias a los modelos estadísticos obtenidos y por medio de la aplicación de la función de deseabilidad integrada en el software Design Expert 11, se determinaron las mejores condiciones de operación en el rango experimental para obtener la mayor área superficial y el mayor rendimiento posible dentro del rango experimental. Se considera que el área superficial específica es un criterio predominante importante para el tipo de producto que se desea obtener del proceso, y no así para el rendimiento másico. Por tanto, se pudo contraponer que los comportamientos de ambas variables respuestas son inversamente proporcionales entre sí. Para subsanar esto se decidió anteponer la respuesta área superficial específica ante la respuesta rendimiento másico. Se determinó así que las condiciones reportadas como las mejores, constituyen una maximización de la respuesta área superficial específica, mientras que la variable rendimiento másico no se maximiza. Además, se consideró que el factor relación en peso de la impregnación representa un costo monetario alto debido a las cantidades elevadas de H3PO4 usadas en las impregnaciones. Por esto, para la optimización del proceso se buscó minimizar este factor. Por tanto, las condiciones de operación más adecuadas determinadas por la optimización mediante la función de deseabilidad corresponden a 600°C para la temperatura, un tiempo de proceso de 4 horas, y una relación en peso de la impregnación de 1:1 de PET: H3PO4.